Spotlight
[Special Contents] Regenerative Electric Assist System FEREMO™
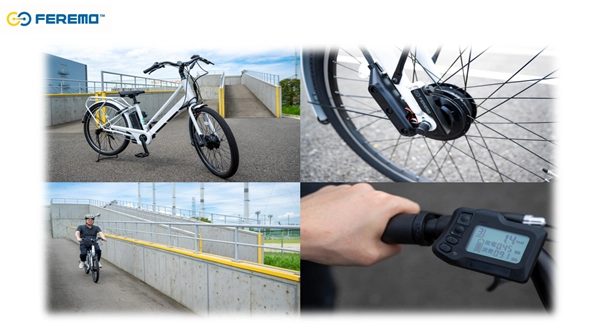
- Solution
- Sustainability
High Reliability Products lineup
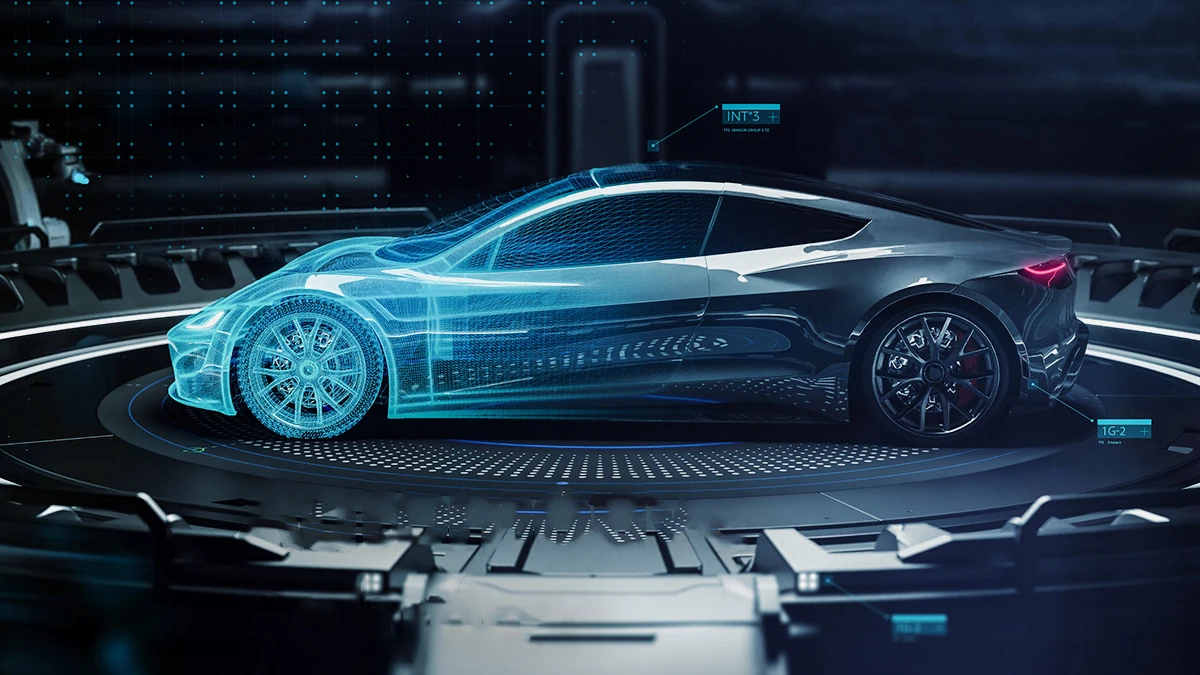
- Product
News
Product Search
- Distributor Inventory Search
- North America
- Europe
- Asia Pacific
- Other Regions
[Special Contents] Regenerative Electric Assist System FEREMO™
High Reliability Products lineup