We report how we worked on the 5Ms set in our Medium-Term Occupational Health and Safety Targets, during the fiscal year 2023.
The report covers TAIYO YUDEN CO., LTD.: six sites, and its domestic and overseas consolidated subsidiaries.
Organizations Covered by this Report
TAIYO YUDEN CO., LTD. (Japan) | Takasaki Global Center / Haruna Plant / Nakanojo Plant / Tamamura Plant / Yawatabara Plant / R&D Center |
---|---|
Consolidated Subsidiary (Japan) | TAIYO YUDEN CHEMICAL TECHNOLOGY CO., LTD. / TAIYO YUDEN TECHNO SOLUTIONS CO., LTD. / FUKUSHIMA TAIYO YUDEN CO., LTD. / NIIGATA TAIYO YUDEN CO., LTD. / WAKAYAMA TAIYO YUDEN CO., LTD. / TAIYO YUDEN Mobile Technology Co., Ltd. / Kankyo Assist Co., Ltd. / ELNA CO.,LTD. |
Consolidated Subsidiary (Other Countries) | South Korea:KOREA KYONG NAM TAIYO YUDEN CO., LTD. China: TAIYO YUDEN (CHANGZHOU) CO., LTD. China: TAIYO YUDEN (GUANGDONG) CO., LTD. Philippines: TAIYO YUDEN (PHILIPPINES), INC. Malaysia: TAIYO YUDEN (SARAWAK) SDN. BHD. Malaysia: ELNA (MALAYSIA) SDN. BHD. Thailand: ELNA (THAILAND) CO., LTD. |
Efforts and Status
Man
- Intensive basic training and fostering “Awareness of safe behavior”
- To create a safe workplace culture, we are conducting activities to help employees increase their knowledge of health and safety so that they can perform their work with such knowledge in mind.
In FY2023, we worked on the challenges identified on the basis of the results of the analysis of the fifth Safety Awareness Survey of the employees working at the sites in Japan. As a result of quantitatively visualizing the effects of protective equipment to workers and strengthening the training on the right way to wear it, it was confirmed in the sixth Safety Awareness Survey that improvements had been made. We also conducted the new Safety Awareness Survey of the employees working at the overseas employees in FY2023, analyzed the survey results, and visualized the challenges.
We will continue to conduct the Safety Awareness Survey and improve safety awareness of each employee to promote a culture of workplace safety.
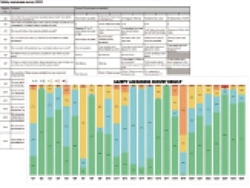
Machine
- Enhancing the level of facility safety design for designers
- With the objective of ensuring our machine safety activities conform to global standards (ISO and IEC), we are reviewing the Safety Standards for Group Machines, which define measures against risks common to production machines to enhance safety measures for them.
In FY2023, we developed a system that enabled us to identify the cause when trouble happened, implement measures, and apply them to other sites more consistently and swiftly by putting the identification labels on all equipment to make it easy to check the implementation status of safety measures of equipment and by centrally managing the results of the assessment conducted on the basis of the equipment safety standards.
We will continue our efforts to reduce occupational injuries associated with machines.
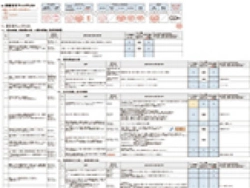
Method
- Safe work without inconsistencies
- We are upgrading and reviewing procedures to standardize them and make them safe and consistent so that employees can work more safely.
In FY2023, we improved the safety levels in the workplace and the management levels for emergency preparedness by analyzing customer needs, industry needs, audit findings, verifying and reviewing the effects of the best practices on inspection of the safety devices of the production facilities and the eye wash stations to be used in an emergency, and standardizing the methods.
We will continue to strive toward promoting a safe working environment from a common perspective.
Material
- Minimization of toxicity and danger of chemical substances
- To minimize the hazards and dangers of chemical substances, we are continuously taking measures against risks associated with tasks that require workers to handle chemical substances.
In FY2023, as a measure against the risk when cleaning the equipment using organic solvents, we verified and reviewed the organic solvents to use and the production method and shifted to less harmful substances to mitigate the risk of the handling chemicals.
We will continue to work toward minimizing the hazards and dangers of chemical substances.
Measurement
- Strengthening of checking system
- To provide safe and hygienic workplaces, we are working to raise check levels by upgrading and improving the methods for identifying invisible hazards (or those that have gone unnoticed).
In FY2023, we verified and reviewed the measures for the risk of falling accidents while walking at each site. We also made efforts to create a safer workplace by identifying new risks from a professional perspective and giving instructions on how to make improvements based on the cases of advanced efforts, as well as confirming the effectiveness of the measures by having the safety and health staff members conduct on-site audits.
Going forward, we will continue our efforts to deepen the level of checks to create safe and hygienic workplaces.
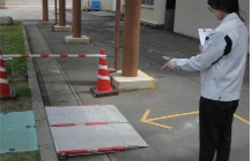
Health
- 1 Reducing incidences of mental health problems
-
Taiyo Yuden developed a system*1 to reduce the number of employees with mental health problems and are making efforts to prevent mental health problems.
In addition to conducting statutory stress checks using the new Occupational Stress Simple Questionnaire, we also conduct surveys on work engagement*2 and the harassment rate in the organization.
As part of the approach to individuals, we made efforts to prevent mental health problems by holding interviews with new employees and mid-career hires whose living environments had changed to check their physical and mental health and by having the industrial nursing staff hold interviews with employees who were suspected of being at high risk of mental health problems. In addition, in this survey, we also conducted the stress check on the employees working at the overseas sites.
As part of the organizational approach, we provided feedback on the results of the group analysis of the stress check results to the persons in charge of each department and discussed measures to implement to improve the workplace environment in order to enhance psychological safety*3 in the entire organization.Thanks to these efforts, the incidence rate remains the same as the previous year at 0.73% (see G1).
We will continue to enhance training, work closely with industrial doctors, psychiatrists, and industrial counselors, and work on mental health care so that all employees can work with peace of mind and motivation.Mental Healthcare System
G1: Incidence rate
-
*2Work engagement is the condition in which employees gain energy from their work and are proud of the work they do, and so are able to work with vigor.
-
*3Refers to the state where you can speak your thoughts and feelings to anyone in the organization with confidence.
-
- 2 Establishing a healthy lifestyle
-
Under the management philosophy, “Employee Well-being,” Taiyo Yuden sees employee health management as a management issue, and is committed to health management in order to create a foundation for safe and secure work, create an organization where employees are motivated, and contribute to productivity and creativity. Within this, to advance these activities both strategically and systematically, we have set health indicators (Focus5: Food, non-smoking, exercise, sleep, and stress) and established targets, and have been endeavoring to implement specific health measures to achieve these targets.
In FY2023, we implemented measures with a special focus on “Exercise” and “Sleep” in the Focus5 indicators.
As part of the “Exercise” measures, we held an event in which participants measured their health status using walking form measurement devices and body composition analyzers, under the theme of “walking” that anyone could practice easily at any time. We visualized participants' walking form, muscle mass, amount of body fat, and other attributes to provide opportunities for them to improve their lifestyle habits by enhancing their daily physical activities. As part of the “Sleep” measures, we conducted e-learning for people having a desk job so that they could correctly understand sleep and held seminars on sleep for shift workers and new employees.
In addition, as shift workers were likely to have sleep problems, we conducted a questionnaire survey of all the employees who worked in shifts to collect information to consider measures for the improvement of the quality of sleep and visualized the challenges. Other measures we implemented include the efforts to quit smoking, improvement of the canteen, and health promotion measures by the Health Insurance Society (walking event).
As a result, in terms of external recognition, we were selected for the Ministry of Economy, Trade and Industry's system Health and Productivity Management Organization 2024 -White 500*4 for the three consecutive years. In addition, as a company that actively works to promote sports activities to promote the health of employees, we were certified by the Japan Sports Agency as a Sports Encouragement Company 2024*5 for the three consecutive years.
We will continue to pursue both mentally and physically healthier work environments that enable our employees to work with vigor.-
*4A program that certifies only the most significant 500 companies in the results of the Survey on Health and Productivity Management.
-
*5A program which certifies companies actively promoting measures to improve employees' health through sports.
-
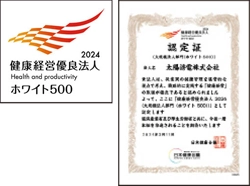
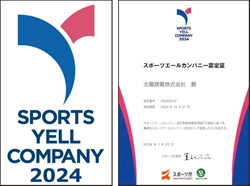