Management System Overview, Promotion Structure
Our group-wide Safety and Environmental Management System keeps individual activities proceeding toward common goals under a common philosophy.
System Overview
This management system consists of long- and short-cycle activities.
In the long-cycle activities, which are designed for the entire group, we are making continuous improvements based on common goals and criteria by checking achievements based on reports about site audits and from sites and by reviewing the management system.
For site-specific short-cycle activities, we have an ISO 14001-compliant management system and the Occupational Health and Safety Management System (OHSMS) in place.
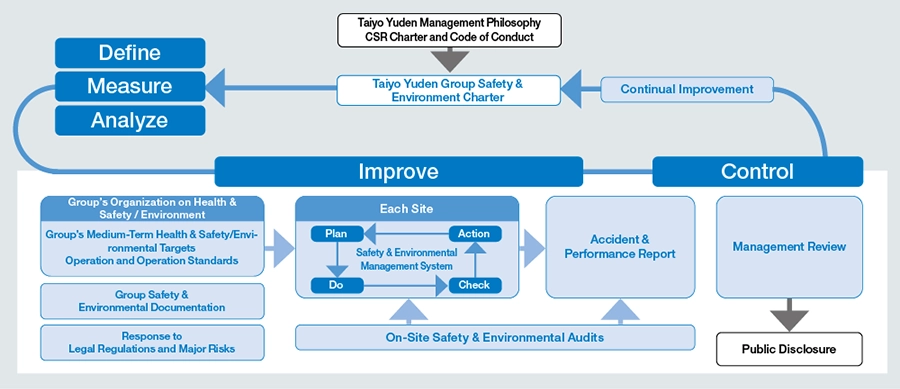
Promotion Structure
The officer in charge of safety and environmental affairs appointed by the President and Chief Executive Officer has overall responsibility for building and managing the promotion structure for Taiyo Yuden's Safety and Environmental Management System.
Safety and Environmental MS Committee, the Environmental Promotion Committee debate and decide policies and issues to be addressed. Each manager of sites then converts his/her decisions into actual plans matching the characteristics of each site, and takes charge of publicizing, enforcing and promoting these concrete targets.
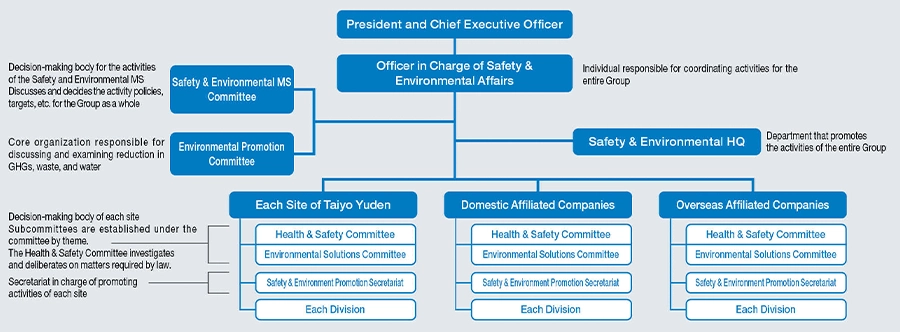
-
*MS stands for the management system.
-
*HQ stands for Headquarters.
-
*The Health and Safety Committee elects company and worker representatives.
Certification Acquisition Status
The Taiyo Yuden Group is ISO 14001 certified for its production sites and development centers.
In addition, we address corporate responsibility in the global supply chain, and the group undergoes the Validated Assessment Program (VAP) audits by the Responsible Business Alliance (RBA) on a continuous basis in line with the set plan.
List of Certifications Acquired
Location | Name of Sites | Acquired ISO14001 Certification | Certification authorities |
---|---|---|---|
Japan | TAIYO YUDEN CO., LTD. Takasaki Global Center,Haruna Plant, Nakanojo Plant, Tamamura Plant, Yawatabara Plant, R&D Center TAIYO YUDEN CHEMICAL TECHNOLOGY CO., LTD. TAIYO YUDEN TECHNO SOLUTIONS CO., LTD. FUKUSHIMA TAIYO YUDEN CO., LTD. NIIGATA TAIYO YUDEN CO., LTD. WAKAYAMA TAIYO YUDEN CO., LTD. TAIYO YUDEN Mobile Technology Co., Ltd. Kankyo Assist Co., Ltd. ELNA CO., LTD. |
4669324 (as of Oct. 1998) Collectively certified in Japan |
BV |
South Korea | KOREA KYONG NAM TAIYO YUDEN CO., LTD. | KR003545 (as of Mar. 2002) | BV |
China | TAIYO YUDEN (GUANGDONG) CO., LTD. | CN042006 (as of Dec. 2001) | BV |
Philippines | TAIYO YUDEN (PHILIPPINES), INC. | PH13/0920 (as of Nov. 2001) | SGS |
Malaysia | TAIYO YUDEN (SARAWAK) SDN. BHD. | EMS00226 (as of Oct. 2002) | SIRIM |
ELNA (MALAYSIA) SDN. BHD. | 17318-E (as of Dec. 2003) | Kiwa | |
Thailand | ELNA (THAILAND) CO., LTD. | 04 104 990506 (as of Mar. 2004) | TUV |
RBA-VAP Audit
TAIYO YUDEN Group has implemented activities to comply with the RBA (Responsible Business Alliance) Code of Conduct, which is a code of conduct related to social responsibility. We regularly have the RBA-VAP audit as third-party evaluation to enhance level of labor, ethics, health and safety, and environment continually. Subjects of the audit are 17 manufacturing sites and 1 non-manufacturing sites*.
TAIYO YUDEN CO., LTD. (Japan) | Takasaki Global Center* / Haruna Plant / Nakanojo Plant / Tamamura Plant / Yawatabara Plant |
---|---|
Consolidated Subsidiary (Japan) | TAIYO YUDEN CHEMICAL TECHNOLOGY CO., LTD. / TAIYO YUDEN TECHNO SOLUTIONS CO., LTD. / FUKUSHIMA TAIYO YUDEN CO., LTD. / NIIGATA TAIYO YUDEN CO., LTD. / WAKAYAMA TAIYO YUDEN CO., LTD. / TAIYO YUDEN Mobile Technology Co., Ltd. (Head Office & Tokorozawa Plant) / ELNA CO., LTD. (Shirakawa Factory/Aomori Factory) |
Consolidated Subsidiary (Other Countries) | KOREA KYONG NAM TAIYO YUDEN CO., LTD. TAIYO YUDEN (GUANGDONG) CO., LTD. TAIYO YUDEN (PHILIPPINES), INC. TAIYO YUDEN (SARAWAK) SDN. BHD. |
Audit
Triple audits evaluate each site's compliance, accident risk management, and the environmental impact situation aimed at producing continuous improvement.
External Audits
- ISO14001 certification audits by certification authorities
- Sites with ISO14001 certification underwent the audits required to update or maintain such certification. These audits uncovered 2 nonconformities. The root causes were analyzed and corrective action was promptly taken in response to each issue. The nonconformities were minor issues related to the management systems and would not cause environmental pollution or accidents.
Number of Nonconformity Instances Found with External Audits
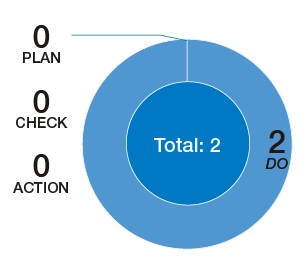
Nonconformity Examples
- Details of nonconformities
- The method to check the measures against static electricity implemented by the supplier when filling the tank with fuel has not been standardized.
- Corrective/remedial actions taken
- The operation standards have been revised to make sure that the implementation status of the measures against static electricity can be checked and that the parties concerned have received training.
- Details of nonconformities
- The amount of the refrigerant was not sufficiently checked when the supplier maintained the refrigeration machine.
- Corrective/remedial actions taken
- The procedures for preventive maintenance of the refrigeration machine have been revised to make sure that the amount of the refrigerant can be checked and that the supplier and the internal parties concerned have received training.
The RBA-VAP audits for FY2023 have been completed at 7 domestic sites and 4 overseas sites.
Internal Site Audits
- Audits of site safety and environmental activities at regularly scheduled intervals allow us to compare sites.
(Domestic sites: Once every two years, Overseas sites: Once every three years) - In FY2023, we performed site audits to examine the status of compliance with customer requirements, the RBA Code of Conduct's safety, health, and environmental requirements.
In each audit, auditors checked documents and performed on-site audits on matters related to customer requirements/RBA requirements such as risk management against potential hazards, management of required protective equipment, emergency preparedness, and management of chemical substances, waste, and air/water quality.
The audits revealed inadequacies including label management, emergency preparedness, management of fire extinguishers.
Countermeasures were implemented for validated inadequacies found during the site audits, and verified its effectiveness.
We aim to improve the level of health, safety, and environmental protection activities for the whole group by globally incorporating societal requirements in a timely manner and sharing the results after benchmarking products from all sites.
Issue Examples
-
Some of the hazard labels(GHS*) on the chemical containers were inadequate.
-
The update and management of the first-aid equipment map were inadequate.
-
Some items on the list of the monthly fire extinguisher self-inspection were inadequate.
-
*The Globally Harmonized System of Classification and Labeling of Chemicals
Internal Audits
- Audits targeting site departments on observance of safety and environment laws, target achievement, and performance.
(Once or twice every year) - All sites conducted internal audits of their departments in accordance with their management systems. Priority areas were determined for each site, and 36 nonconformities were uncovered as a result of conducting internal audits (at sites in Japan).
Corrective action was completed in all cases without delay, and after a follow-up check, it was reported to the managers that the management system has been effective in complying with the Taiyo Yuden Group’s policies and goals.
Other Audits
On-site inspection of waste disposal contractors (Sites in Japan)
During FY2023, we inspected and audited 34 companies (19 collection, delivery, and intermediate processing companies; and 15 intermediate processing companies). The results showed that all inspected operators are processing and disposing of waste appropriately. The operators have also been classified into three ranks from the results of these inspections, with the frequency of future inspections varying depending on the rank of the operator.
Training
We provide a variety of training programs covering both general and specialized knowledge to promote employees' awareness of preventing occupational injury and illness, as well as active participation in environmental conservation.
Training Structure
Name | Category | Purpose | Main Subjects | |
---|---|---|---|---|
General Training | Training for new recruits | Awareness | Raising new recruits' awareness of occupational health and safety and environmental preservation, and ensuring they understand environmental problems pertinent to companies | General theory of Safety, Health, and Environment/ Status of Safety, Health, and Environment at the Taiyo Yuden Group |
General training | Deepening all employees' understanding of the Taiyo Yuden Group Safety, Health, and Environment Charter and Course of Action, and teaching them the skills to act accordingly | Management system (including the Safety, Health, and Environment Charter) / Mental health | ||
Workplace training | Understanding potential hazards and environmental impact with regard to divisional health and safety/environmental activities and work |
Division activities / Matters for compliance in work | ||
Health & Safety Training | Training for managers, instructors and supervisors | Abilities | Deepening understanding of the role of the duty for employee safety required by legal regulations and teaching foremen skills to instruct their subordinates regarding health and safety. | Role of the General Manager of Health and Safety / Role of management / Role of foreman / Chemical substance management/Hazardous material management |
Training for specialists | Teaching of specialized skills to operators of forklifts, cranes, and other heavy equipment, as well as managers of processes that handle organic solvents and the like, and employees involved in these tasks | Workplace restricted duties / Training for specific tasks / Prevention of static electricity accidents | ||
Training for risk assessors | Teaching the skills to recognize risks and creating a safe and sanitary workplace | Risk assessment/Health and Safety targets / Cases of Health and Safety improvements / Causes of Health and Safety accidents and their countermeasures | ||
Environmental Training | Training for specialists | Teaching special skills to managers and relevant employees involved with equipment and facilities for which a legal notification is required | Management to prevent deterioration of water quality / Management to prevent air pollution/Waste management | |
Specialized training | Training skills to integrate business activities with environmental activities in order to balance an improvement in our environmental impact with improved resource productivity | Chemical substances and their environmental impact /Environmental targets/Cases of environmental improvements/Causes of environmental accidents and their countermeasures |
Training Examples
General Training
- Holding events related to health and safety
- We hold various events related to health and safety at all sites and these events provide opportunities for employees to raise their awareness and develop their abilities. For example, the walking form evaluation with the aim of preventing and relieving lower back pain while walking, the workshop on heat stroke prevention, and other training programs were conducted.
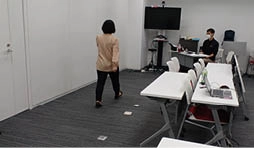
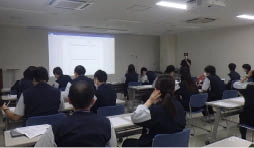
Occupational Health and Safety Training
- Training on how to wear the respiratory protective equipment
- We conducted training to learn the right way of wearing mask by measuring the fitness between the mask and the face in real time.
- High-pressure gas safety training
- The training on the properties and dangers of high-pressure gas and the daily monitoring and inspection methods was conducted to prevent accidents caused by high-pressure gas equipment.
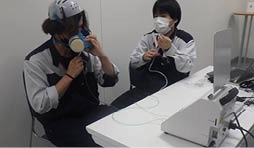
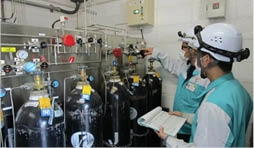
Environmental Training
- Training for wastewater treatment facility managers
- The training on the wastewater restriction standards and maintenance of the wasterwater treatment control system including on-site practice was conducted for the wasterwater treatment facility managers.
- Training for waste management personnels
- The training on the classification of waste, the Manifest System and how to manage waste disposal vendors was conducted to promote the proper management of waste.
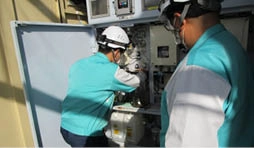
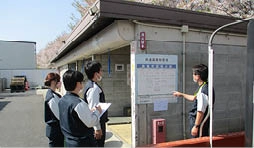